The Car is the Star
GT40 - Where Sheer Power Met Reliability
The car that won the 1966 Le Mans, not only for Ford, but for America. Employing the world’s finest minds and talent, Henry II set out to crush Ferrari and he did so, badly, with a 1-2-3 finish. These are the specs, nuances, development and overall history of chassis P/1046.
The design of the GT40 Mk. II was carefully constructed after hours and hours of purposeful attention to lightweighting, strengthening and aerodynamics. It wasn’t until the ‘60s that aerodynamics was truly studied in race cars eclipsing 150-200 MPH. Enzo Ferrari had the mindset that if a car couldn't go faster, it needed more horsepower. Ford engineers knew both horsepower and aerodynamics win races.
Ford came up with their early GT design in Dearborn by looking at what the competition was doing. Formula One cars of the day were well constructed and employed lots of technology, but were fuel tanks on wheels. It wasn’t until 1962 when Lotus designed the first monocoque chassis with the model 29. The Lotus 29 was a rear engine 4.2L Ford powered 370 hp V8 in an aluminum monocoque designed chassis that had Girling disc brakes, a 4-speed transmission, 6- and 7-inch tires and weighed only 1,170 pounds. The car, as advanced as it was, had absolutely no "aerodynamics" or active & passive safety considerations in it's design.
Considered to be technologically advanced for its day, modern Ford engineers tested a 1969 Le Mans winner from their museum when they decided to resurrect the classic ‘60s GT40 as a limited-production high-end sports car. What they discovered in their high-tech wind tunnel was that the GT40 had, in the words of Ford aerodynamicist Kent Harrison, “an incredible amount of front-end lift.”
It wasn’t until the ‘60s that aerodynamics was truly studied in race cars eclipsing 150-200 MPH.
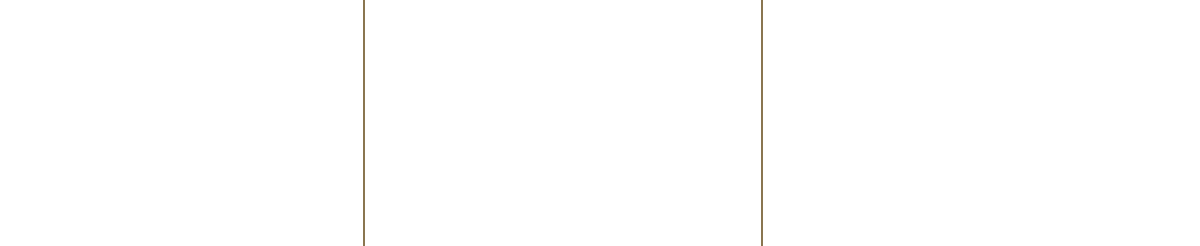
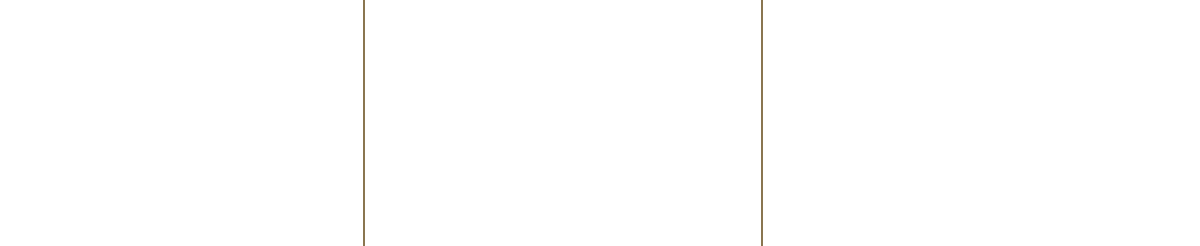
The GT40’s extraordinary power-to-weight, coupled with its reliability, were the determining factors in the car’s ability to win the 24 Hours of Le Mans.
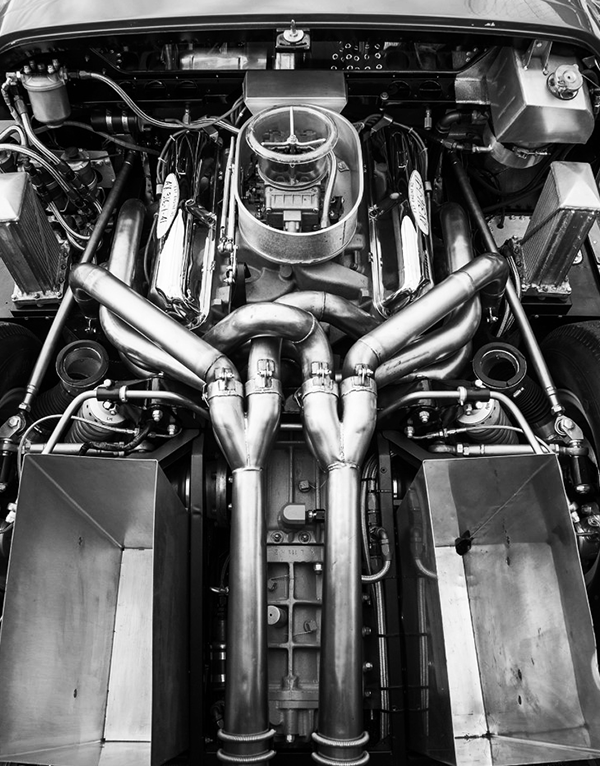
CID - | 427 |
Bore x Stroke - | 4.2346 x 3.784 |
Connecting Rod Length - | 6.488 |
Horsepower @ rpm - | 485 @ 6200-6400 |
Torque @ rpm - | 474.5 @ 3200-3600 |
Compression Ratio - | 10.5:1 |
Carburetion BBL - | 1 x 4-bbl |
Carburetor - | Modified Holley 780 cfm |
Lifters - | Mechanical |
Rocker Arm Ratio - | 1.76:1 |
Valve Lift (in/ex) - | 0.527/0.527 |
Valve head Dia (in/ex) - | 2.060/1.625 |
Cylinder Head Material - | Aluminum |
Cam Specs (in/ex/overlap) - | 342/324/96 |
The Powertrain
Thousands of hours of testing were completed before engine number AX316-1-41 was built built and fitted into chassis P/1046. It was Ford’s 427 FE 90-degree OHV V8 engine pulled from the Ford Galaxie (used in NASCAR at the time). There were a few reasons why Roy Lunn, the godfather of the GT40, opted for the powerplant. After unsuccessful campaigns with the 255ci and 289ci engines, the logical next step was to throw in a big block, but that presented major design concerns.
Engineers were concerned about ground clearance, cooling, intake and exhaust clearances, oil capacity, fuel handling, durability and driveability. However, in the end as you may know, all the hours spent testing and fitting paid off. One reason due to having access to a dynamometer. Without this, real world testing may have been almost obsolete. Ford didn’t have access to the track, so the dynamometer helped Ford simulate a 24-hour run of the Le Mans circuit. This allowed Ford engineers to test the engine and driveline units and simulate the on-course throttle, clutch and shift patterns of the company’s race engines. Thus, in addition to the larger engine and more reliable engine, Ford used forward-thinking and technology to dethrone the prancing horse.
Outsmarting the Competition: The Dynamometer
Ford didn’t have access to the track, so the dynamometer helped Ford simulate a 24-hour run of the Le Mans circuit.

The Interior
Chris Amon was quoted as saying, "The interior was quite comfortable, as much as a race car can be, compared to other race cars I have driven.”
- Instrumentation:
- 7000 RPG Tach
- Oil Temp
- Water Temp
- Fuel Pressure
- Ammeter
- Gearbox
- Warning lights:
- Differential Oil Pressure
- Engine Oil Pressure
- Right Hand Drive
- Perforated seating to keep drivers cool